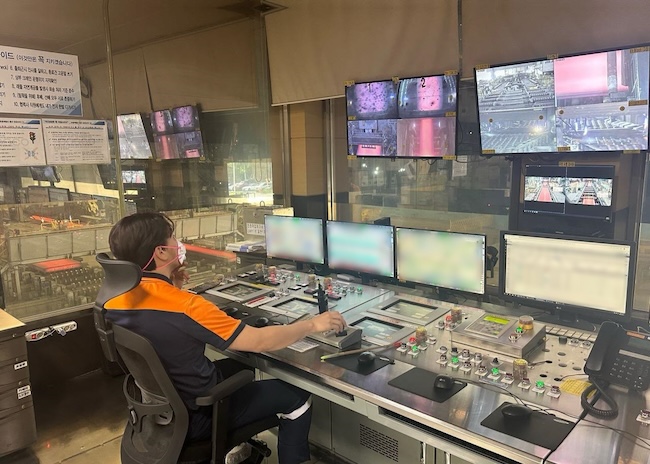
Smart CCTV systems monitor the movement of 35-ton, 1,000°C slabs along conveyor belts. (Image courtesy of POSCO DX)
POHANG, Aug. 26 (Korea Bizwire) – On a sweltering August day, the POSCO steel mill in Pohang hums with activity. But it’s not just human workers feeling the heat — artificial intelligence is taking on some of the most challenging and dangerous tasks in this sprawling industrial complex.
At a product inspection area about 15 minutes by car from the main gate, a fleet of smart CCTV cameras springs into action as a large trailer truck carrying 14 coils of wire rod enters. The AI-powered cameras on both sides of the vehicle busily scan barcodes and text on labels affixed to each coil.
This automated process, implemented earlier this year in collaboration with POSCO Group’s IT subsidiary POSCO DX, verifies that the production information in the manufacturing execution system (MES) matches the actual products loaded for shipment to domestic and international customers.
“Previously, inspectors had to manually check about 3,000 wire rod labels against MES records daily, which sometimes led to errors,” explained a POSCO representative.
“There were also safety concerns, as inspectors occasionally had to climb onto vehicles to view labels on the opposite side of the load.”
The new system, which went live after a six-month testing period in July of last year, has eliminated these risks and inaccuracies. Twenty-four label-reading cameras and two license plate recognition cameras now operate in the inspection area’s A and B buildings.
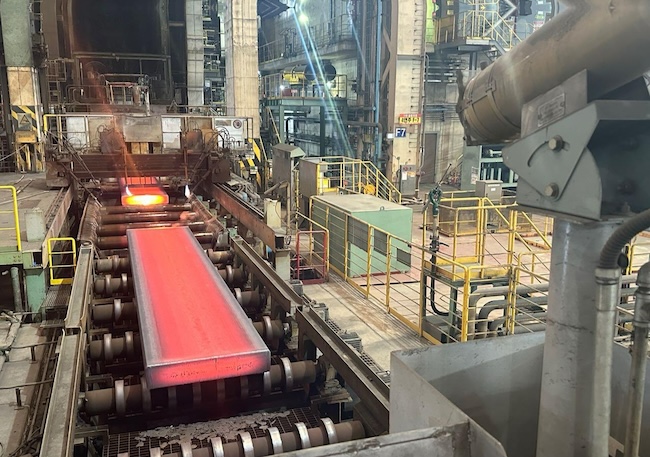
Smart CCTV systems monitor the movement of 35-ton, 1,000°C slabs along conveyor belts. (Image courtesy of POSCO DX)
But the reach of AI at POSCO extends far beyond mere product verification. In the continuous casting plant, where molten iron is solidified into semi-finished slabs, AI acts as a vigilant guardian against potentially catastrophic accidents.
Smart CCTV systems monitor the movement of 35-ton, 1,000°C slabs along conveyor belts. If a slab begins to misalign — a situation known as “snaking” — the AI can not only alert operators but also autonomously halt the production line.
“We produce about 400 slabs per day, and the AI intervenes to stop the equipment about five or six times a month,” said Park Joong-hae, a manager in POSCO’s production technology department.
“To prevent accidents, we manage with stricter criteria, so the number of stoppage events is much higher.”
Since the smart CCTV system’s introduction in 2021, there have been no slab misalignment incidents. This has freed staff from the monotonous task of constant monitor surveillance and significantly improved workplace safety.
Even the massive 1,000-ton locomotives that transport molten iron throughout the complex are now under AI supervision.
POSCO DX has developed an AI solution that analyzes CCTV footage around railroad crossings, alerting train operators to potential hazards like workers or vehicles in the vicinity.
To combat the challenges posed by frequent coastal fog, POSCO DX partnered with POSTECH (Pohang University of Science and Technology) to create technology that removes fog and dust from CCTV images, ensuring clear visuals for AI analysis even in adverse weather conditions.
“Industrial AI can help address quality inconsistencies that arise from variations in worker skill levels,” said Yoon Il-yong, head of POSCO DX’s AI Technology Center.
“Based on our understanding of steelmaking environments and operational know-how, we’re focusing on replacing tasks that don’t necessarily require human involvement and hazardous on-site work with AI. This will contribute to transforming steel mills into intelligent factories.”
Kevin Lee (kevinlee@koreabizwire.com)