
Utilizing modular construction techniques to build a new apartment complex in Sejong City’s 6-3 Living Area (Image courtesy of the Korea Land and Housing Corporation)
SEJONG, Jul. 9 (Korea Bizwire) – In a significant development for South Korea’s public housing sector, the Korea Land and Housing Corporation (LH) is utilizing modular construction techniques to build a new apartment complex in Sejong City’s 6-3 Living Area.
This innovative approach promises to revolutionize the construction industry by significantly reducing build times and maintaining consistent quality standards.
On July 4, at the construction site in Sanul-dong, a massive crane hoisted a 23-ton modular unit measuring 11.3 meters in length and 3.3 meters in width to its designated position on the fourth floor.
Each of these box-like modules takes approximately 30 minutes to place. Once all 575 units are stacked and secured, they will form a seven-story apartment complex comprising 416 households.
Modular construction involves pre-fabricating individual living spaces, complete with walls, windows, plumbing, and bathrooms, in a factory setting before assembling them on-site. This method allows for over 80% of the construction process to occur off-site, under controlled conditions.
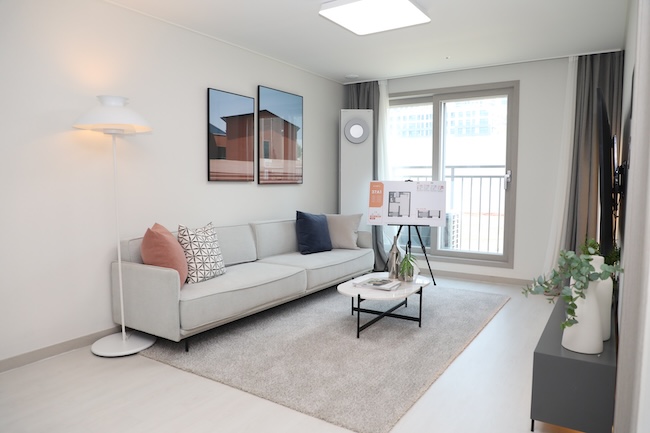
Utilizing modular construction techniques to build a new apartment complex in Sejong City’s 6-3 Living Area (Image courtesy of the Korea Land and Housing Corporation)
The modules used in the Sejong public housing project are manufactured in a factory in Gunsan and transported to the site via trailer. The units installed on the day of observation were designed for single-person households, with a floor area of 21 square meters.
These come fully equipped with kitchen sinks, built-in cabinets, and finished flooring. Larger 37-square-meter units are created by connecting two modules seamlessly.
One of the primary advantages of modular construction is the reduction in on-site construction time by approximately 30% compared to traditional reinforced concrete methods. Module installation for the project began in June, and is scheduled for completion in December of this year.
However, the modular approach currently faces challenges in South Korea, primarily due to the lack of a large-scale production system, resulting in higher construction costs. At present, modular construction is about 30% more expensive than traditional methods.
LH President Lee Han-joon emphasized the necessity of expanding modular housing due to the difficulties in finding construction workers. “LH will increase the volume of modular housing, focusing on public housing, to achieve economies of scale,” Lee stated.
LH claims that modular homes can last up to 100 years with periodic component replacements, in contrast to conventional apartments that typically face reconstruction discussions every 30 years. The design also offers advantages in reducing noise between floors.
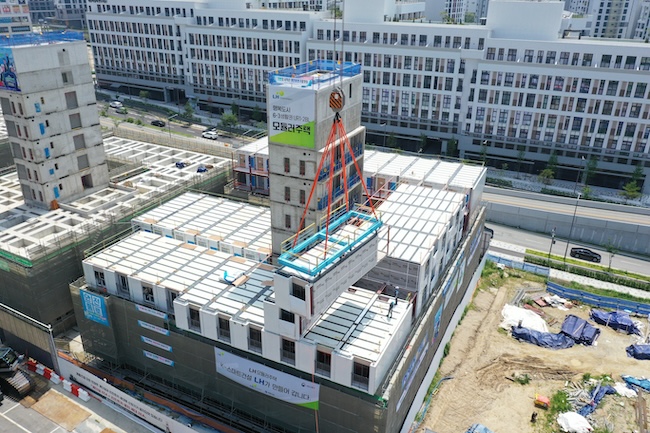
Utilizing modular construction techniques to build a new apartment complex in Sejong City’s 6-3 Living Area (Image courtesy of the Korea Land and Housing Corporation)
The corporation is pushing the boundaries of modular construction, with plans for a 12-story, 450-unit complex in Sejong’s Smart City pilot area and a 20-story, 381-unit building in Uiwang, Gyeonggi Province, which would be the tallest modular structure in South Korea.
To further develop the modular housing market, which reached 805.5 billion won in value last year, LH has formed partnerships with various organizations and companies to standardize designs and improve production capabilities.
Despite its potential, the growth of modular housing in South Korea is hindered by regulations designed for traditional construction methods. Industry experts point out that countries where modular construction is more prevalent offer incentives such as relaxed building standards, streamlined permit processes, and tax benefits.
As part of its commitment to innovative construction techniques, LH is also piloting the use of Precast Concrete (PC) methods, which involve manufacturing key concrete components in factories before on-site assembly.
LH aims to eventually use modular and PC methods for about 10% of its annual public housing construction projects, marking a significant shift in the country’s approach to addressing housing needs.
M. H. Lee (mhlee@koreabizwire.com)