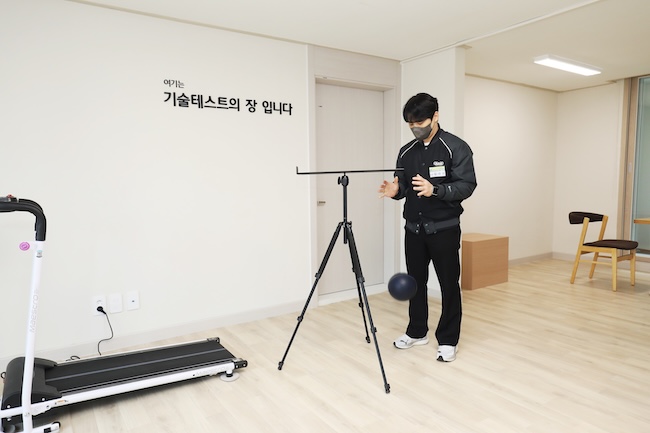
The lab’s name reflects the ambitious goal of achieving noise levels as low as 35 decibels—comparable to a quiet library—setting a benchmark for what is considered the highest standard for floor soundproofing. (Image courtesy of Korea Land and Housing Corporation (LH))
SEOUL, Nov. 25 (Korea Bizwire) — In an effort to tackle persistent floor noise issues in apartments, Korea Land and Housing Corporation (LH) unveiled the country’s largest soundproofing testing facility, the ‘Decibel 35 Lab,’ located at the Sejong Housing Performance Research and Development Center.
This new facility simulates real apartment environments, allowing for in-depth testing of floor structures designed to reduce inter-floor noise.
The lab’s name reflects the ambitious goal of achieving noise levels as low as 35 decibels—comparable to a quiet library—setting a benchmark for what is considered the highest standard for floor soundproofing.
The “Grade 1” floor structure, which minimizes sound transmission from light impacts, like chairs being moved, or heavier impacts, such as children jumping, is designed to produce noise levels below 37 dB, significantly improving on previous standards.
The new floor system is a result of over 1,300 field tests and improvements in materials, such as thicker concrete slabs (210mm to 250mm) and denser mortars to improve noise absorption. These innovations make the floors more effective in reducing the transmission of noise, benefiting residents in both public and private housing.
Starting in the second half of 2025, LH plans to incorporate this advanced technology in the design of all public housing projects, including those in the three new towns under development.
This initiative is expected to not only raise the quality of living in apartments but also set a standard that could lead to broader industry adoption. LH is also opening the Decibel 35 Lab to small and medium-sized enterprises (SMEs) without their own testing facilities, aiming to foster innovation in the construction sector.
Kim Byeong-mun, LH’s Housing Performance Improvement Team Leader, emphasized that the lab would accelerate the verification and dissemination of new technologies, reducing the time required for certification from over a year to just six months.
Despite the benefits, the new noise-reduction floors come with higher construction costs. The thicker slabs and advanced materials increase costs by approximately 400,000 KRW per unit, compared to lower-grade floors.
However, LH officials are exploring ways to offset the increased costs through efficiency improvements, rather than passing them on to consumers.
LH President Lee Han-jun highlighted that further research is underway to develop technologies for even thinner floors that meet noise standards, which could significantly reduce costs while addressing inter-floor noise.
Other noise-related challenges, such as wall noise and plumbing sounds, still remain significant issues in apartment living. In response, LH plans to introduce in-unit plumbing systems, reducing the need for pipes to pass through floors, which should help cut down on plumbing-related noise.
The corporation is also introducing a new system called ‘NoiseGuard,’ which alerts residents when noise exceeds a certain threshold, encouraging them to reduce disturbances.
While the new systems are initially being tested in existing apartment buildings, LH plans to fully integrate these noise-reduction technologies into future public housing projects, further enhancing the quality of life for residents.
As Korea’s housing sector moves toward more advanced, noise-reducing solutions, LH’s efforts are seen as a key step in improving apartment living standards and making strides toward more sustainable, peaceful residential environments.
Ashley Song (ashley@koreabizwire.com)