
The evolution currently under way in the automotive parts industry is three-pronged: light-weight, eco-friendly, and intelligence.(image:Bjarne Becker@flickr)
SEOUL, Korea, Jan 07 (Korea Bizwire) – Efforts by auto makers and parts makers to introduce more and more parts and components lighter in weight in the car have been long-standing. In the past, however, there were many suggestions within the industry that one can improve fuel efficiency through many different ways than lighter-weight parts. But now the auto makers themselves set out to initiate programs to enhance fuel economy by applying lighter parts from the stage of design to processing and to modulization.
Light-weight
Let us find out in what parts of the car one can reduce the weight most. The car’s weight is distributed almost equally between the body-in-white, powertrain, and chassis, with the highest possibility of cutting weight in these areas. Of these, the powertrain is hard to tinker with as it has many moving parts withstanding extremely high temperature.
The light-weight materials that can be best applicable to the body-in-white and chassis include advanced high-strength steel, aluminum, magnesium, and carbon fiber material. Even though each item has strengths and weaknesses, there is no single item that is best suited to all parts. The advanced high-strength steel is most familiar with car makers and thus low in risk when it comes to application because the material does not require new equipment and machinery. Given most large-scale auto manufacturers have steel units under their wings, it is natural for them to consider advanced high-strength steel as the preferred material for the future.
But there are weaknesses. For example, the specialty steel is somehow limited in application and the range of weight reduction as it is after all steel, with only 10 to 20 percent of room for improvement. In order to overcome this limitation, one must consider radically different solutions, such as aluminum alloys or plastic sandwich steel plates.
Aluminum is excellent is the possibility of weight reduction as much as 40 percent, with desirable properties such as resistance to corrosion and abundance as a subsoil resource. Given per-unit price of aluminum is about 30 percent higher than steel, many auto makers believe aluminum is a material worth trying to experiment with. In addition, car makers in industrialized countries will find aluminum an attractive alternative to steel as most of these countries will soon introduce a scheme to demand producers to take full responsibility of resources they use in their products, which will raise the ratio of aluminum recycling substantially that will again lower production cost.
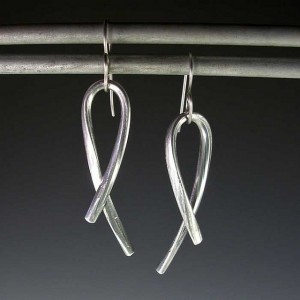
Aluminum is excellent is the possibility of weight reduction as much as 40 percent, with desirable properties such as resistance to corrosion and abundance as a subsoil resource. (image:Mckenna and Currents@flickr)
According to the U.S. Aluminum Association, the percentage of aluminum in a car has increased rapidly to 8 percent of the total weight (on average 156 kilograms) in 2012 from about 2 percent (40 kg) in 1975. Most aluminum applications are used in the engine and related parts, wheels, powertrain, and chassis. Audi has been a leader in using aluminum in their cars. In 1994 the company successfully introduced the A8 with a higher percentage of aluminum and could reduce the car’s weight by 92 kg, or 4.4 percent. Other car makers such as Ford and Toyota have experimented with aluminum for their high-end models, while Tesla and BMW use aluminum in their electric models such as Model S and i3.
Another alternative for car makers is carbon-fiber-reinforced polymer, which is very high in strength but light in weight. It has been a choice application for spacecraft, aircraft, supercars, golf clubs, and large-sized wind blades. As the material doesn’t involve any mining or oil exploration activities, it is environmentally friendly and there is no worry for resource depletion. But its biggest weakness is high price and low productivity in producing the polymer. The price is about 20 times more expensive than steel. The epoxy resin, the base material for carbon-fiber-reinforced polymer, takes too much time to harden after molding, which lowers the productivity and thus raises cost.
Most car makers have stayed away from this material for so long because of these downsides. But BMW has introduced in 2013 the electric car i3 with the life module made with carbon-fiber-reinforced polymer. The company will launch the i8, the plug-in hybrid electric vehicle, in 2014 that embodies the same technology. BMW estimated that it could save the car weight by more than 300 kg from adopting the material for the electric vehicle’s life module and drive module.
Eco-friendly
The attempts by auto makers to use biotech materials for their parts and components have been very recent. During the mid-2000s, Mercedes-Benz tried the first time to apply eco-friendly materials in its high-end line-ups, followed in the late 2000s by Ford and Toyota. Although the first attempt stopped short of using biotech materials for decorative and marketing purposes only, car makers now are intensifying their efforts to expand the application to all areas of auto parts.
For example, conventional bio-materials such as polylactide are used in interior purposes such as the console box or the headliner. But the application is limited because of high cost as well as properties like low durability and low heat resistance. Other environmentally superior materials are the bio-PET (polyethylene terephthalate) and bio foam, which are used for car seat foam and floor mats.
The third kind of bio material is the high-performing bioengineering plastic. Although its price is still high, many car makers believe that this is doable given the new material will be able to replace high-priced parts and components and have many other applications outside the automobile industry. Companies like DuPont and Royal DSM are currently leading the market in this area.
Intelligence
Several auto makers are attempting to apply intelligence or specialty functionalities in their cars as a way to differentiate their models from others. One of such attempts is the “solar roof” offered by Toyota in its Prius electric car. With the solar panel installed on the upper part of the car, the car maintains a proper level of temperature by allowing internal air to circulate as needed. The solar roof can also allow the driver to turn on the air-conditioner remotely so she won’t have to sweat as soon as she gets in the car.
One of the technological trends under way in the auto industry is the use of the head-up display, or HUD, that permits the motorist to view critical information on driving conditions, such as the speed, map, and traffic conditions, on his car’s windshield window or a separate HUD panel. Although it sounds like Mission Impossible the movie, the application is already in place in cars such as Kia’s K9 and Hyundai’s Genesis. In addition, there is an experiment going on to “self-repair” the car’s exterior when it is dented or scratched without involving expensive coating. Toyota has introduced a solution to use stickers to recoat the damaged part. Other auto makers relied on coating materials that can self-repair the surface with an application of heat.
Technology (Follow us @Technews_Korea)