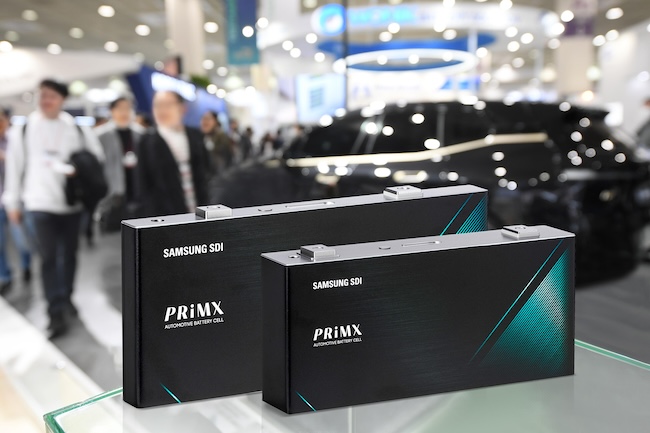
Samsung SDI, which has been the sole supplier of prismatic batteries among South Korean manufacturers, is also seeing increased demand. (Image courtesy of Samsung SDI)
SEOUL, Aug. 6 (Korea Bizwire) – In a significant shift for the electric vehicle (EV) industry, South Korea’s leading battery manufacturers are ramping up production of prismatic batteries, responding to growing market demand and evolving consumer preferences.
LG Energy Solution, a major player in the global battery market, has formed a task force dedicated to developing prismatic batteries and is in discussions with potential customers.
The company, which pioneered cylindrical battery technology in the 1990s, already possesses the technical expertise for prismatic cells.
LG had previously produced smaller prismatic batteries for smartphones and laptops until the late 2010s but discontinued production as consumer demand waned.
If LG Energy Solution proceeds with mass production of prismatic batteries, it would become the first global battery manufacturer to offer all three major form factors: pouch, cylindrical, and prismatic cells.
SK On, another key player in the battery industry, completed its prismatic battery technology development early last year and is preparing for mass production.
Kim Kyung-hun, SK On’s Chief Financial Officer, stated during a recent earnings call, “We have completed the technical development of the prismatic form factor and are in specific discussions with multiple customers regarding production timelines.”
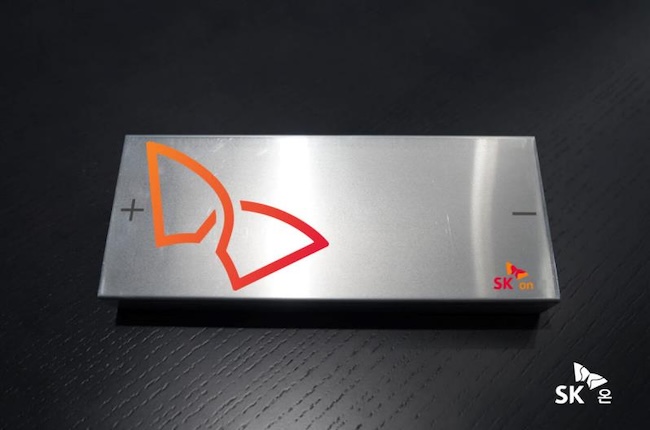
SK On, another key player in the battery industry, completed its prismatic battery technology development early last year and is preparing for mass production. (Image courtesy of SK Innovation)
Samsung SDI, which has been the sole supplier of prismatic batteries among South Korean manufacturers, is also seeing increased demand.
Son Michael, head of the large-scale battery strategic marketing division at Samsung SDI, noted, “We anticipate an expansion in the share of prismatic batteries in the EV market, and we’re experiencing a rise in collaboration requests from OEMs.”
The surge in popularity of prismatic batteries is particularly evident in the European market.
According to market research firm SNE Research, prismatic batteries accounted for 49% of battery usage in Europe last year, up from just 19% in 2019.
This significant increase of 30 percentage points in four years underscores the rapid shift in market preferences.
German automaker Volkswagen has announced plans to adopt prismatic batteries in 80% of its electric vehicles by 2030, further cementing the form factor’s growing importance.
The increased preference for prismatic batteries is largely attributed to their enhanced safety features.
Enclosed in rigid casings, these batteries offer superior durability and resistance to external impacts.
They also feature various safety mechanisms, including vents for gas release and fuses to cut off current flow under specific conditions. The design allows for better heat dissipation, making them optimal for thermal management.
However, prismatic batteries are not without drawbacks. They tend to be heavier and have lower energy density compared to pouch and cylindrical cells, potentially resulting in shorter driving ranges for EVs.
Industry analysts suggest that the current “chasm” in EV demand may be contributing to the popularity of prismatic batteries.
Their simpler manufacturing process and lower production costs make them advantageous for mass production.
Additionally, prismatic cells are well-suited for cell-to-pack (CTP) design, a process that eliminates the need for separate modules, thereby increasing energy density and reducing costs.
Kevin Lee (kevinlee@koreabizwire.com)