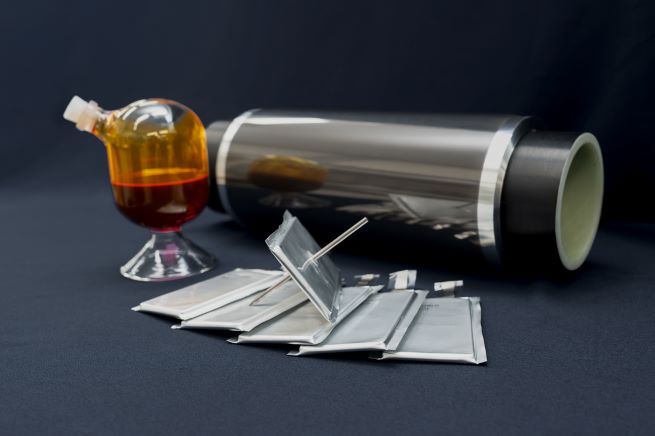
This file photo provided by LG Chem Ltd. shows a Safety Reinforced Layer (SRL), a temperature-responsive material to suppress thermal runaway in batteries. (Yonhap)
SEOUL, Oct. 1 (Korea Bizwire) – In a significant breakthrough for electric vehicle safety, LG Chem, one of South Korea’s leading chemical companies, has announced the development of a new material that could potentially prevent battery fires by cutting off electrical flow when temperatures rise abnormally.
The innovation, described as a “thermal runaway inhibiting material,” functions similarly to a fuse, responding to temperature changes to boost battery safety.
This development, published in the September issue of the prestigious journal Nature Communications, represents a major step forward in addressing one of the most pressing concerns in the electric vehicle industry.
“This is a tangible research outcome that can be applied to products in a short time, even to mass production processes,” said Lee Jong-gu, Chief Technology Officer at LG Chem. “We will continue to advance our safety improvement technology so that customers can use electric vehicles with peace of mind.”
The material, developed by the research team at LG Chem’s Advanced Materials Research Institute, is a composite substance that changes its electrical resistance in response to temperature.
It is designed to be integrated into batteries as an ultra-thin layer — about one-hundredth the thickness of a human hair — between the cathode and the current collector.
When battery temperatures rise to abnormal levels between 90 and 130 degrees Celsius, the material’s structure changes, inhibiting the flow of current.
For every one-degree increase in temperature, the electrical resistance rises by 5,000 ohms, allowing for a rapid response to potential thermal events.
Thermal runaway, a primary cause of electric vehicle battery fires, occurs when the battery’s internal components make unintended contact, leading to a short circuit and rapid temperature increase.
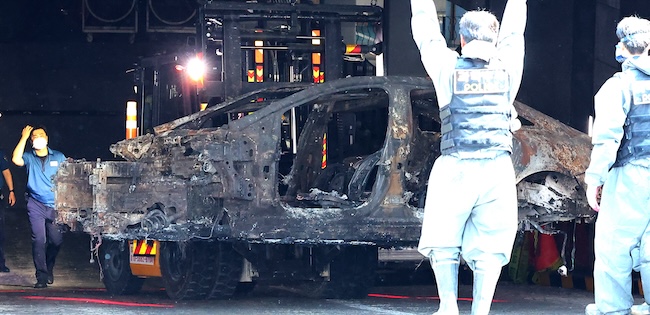
Police move an electric Mercedes-Benz sedan from the underground parking lot of an apartment building after completing their probe in Incheon, 27 kilometers west of Seoul, on Aug. 5, 2024. A fire broke out in the car after it exploded on Aug. 1, resulting in 22 residents and a firefighter being hospitalized. Around 40 cars were burned, and an additional 100 cars in the parking lot were damaged. (Image courtesy of Yonhap)
By interrupting this process in its early stages, LG Chem’s new material could significantly reduce the risk of fire.
The effectiveness of the material was demonstrated through rigorous testing. In experiments with mobile device batteries, those equipped with the new material showed no instances of fire when punctured, compared to a 16% fire rate in standard batteries.
For larger electric vehicle batteries, impact tests resulted in no fires in 70% of cases and quickly extinguished flames in the remaining 30%, a marked improvement over conventional batteries which all caught fire under similar conditions.
LG Chem has completed safety verification tests for mobile device batteries and plans to continue testing on large-capacity electric vehicle batteries through next year.
The company’s achievement is particularly notable for addressing previous challenges in reaction speed and energy density reduction while maintaining compatibility with existing production processes.
Kevin Lee (kevinlee@koreabizwire.com)